Mini-Cubes has used CRP’s carbon reinforced nylon laser sintering material to build small scale satellites.
Founded in 2018, Mini-Cubes is aiming to take the concept of a PocketQube and develop it into a viable product.
A PocketQube is derived from the concept of a CubeSat, a format for small scale satellites that fit within a 50mm x 50mm x 50mm volume and have a mass of less than 25grams, typically used for research purposes (there’s more on PocketQubes here).
According to Joe Latrell, CEO of Mini-Cubes, his team did this on the principle that virtually anyone can reach space today.
With PocketQube satellites, they hope to achieve a better grasp on resource monitoring and give the public a chance to be among the stars.
The Mini-Cubes team started a new project based on a new 1P PocketQube flight-ready, named Discovery.
They turned to CRP USA for the manufacture of the entire satellite frame using additive manufacturing – having worked with additive processes to prototype rocket fins at an aerospace company.

The project
The primary objective of the project was to build a proof of concept for satellites this small.
Latrell explains: “We wanted to include a camera for visual observation, again just to see if it could be done.
“If the process works, we see using the technology to create a constellation of PocketQube satellites just for monitoring a specific resource. In our case that resource is water.
“When we started working on Discovery, I knew I wanted to push the boundaries of what was possible – everything from the small satellite form factor to the technology used to make it.”
For this reason the Mini-Cubes team involved CRP’s USA team and their director of operations, Stewart Davis.
“I knew that with their expertise and experience in the sector, they would be the ultimate technological partner for the project,” explained Latrell.
Challenges to overcome with carbon reinforced nylon laser sintering material
The main challenges were related to the small dimension of the satellite and to the material – since it was the first time that an entire satellite would be built from a Carbon-composite material.
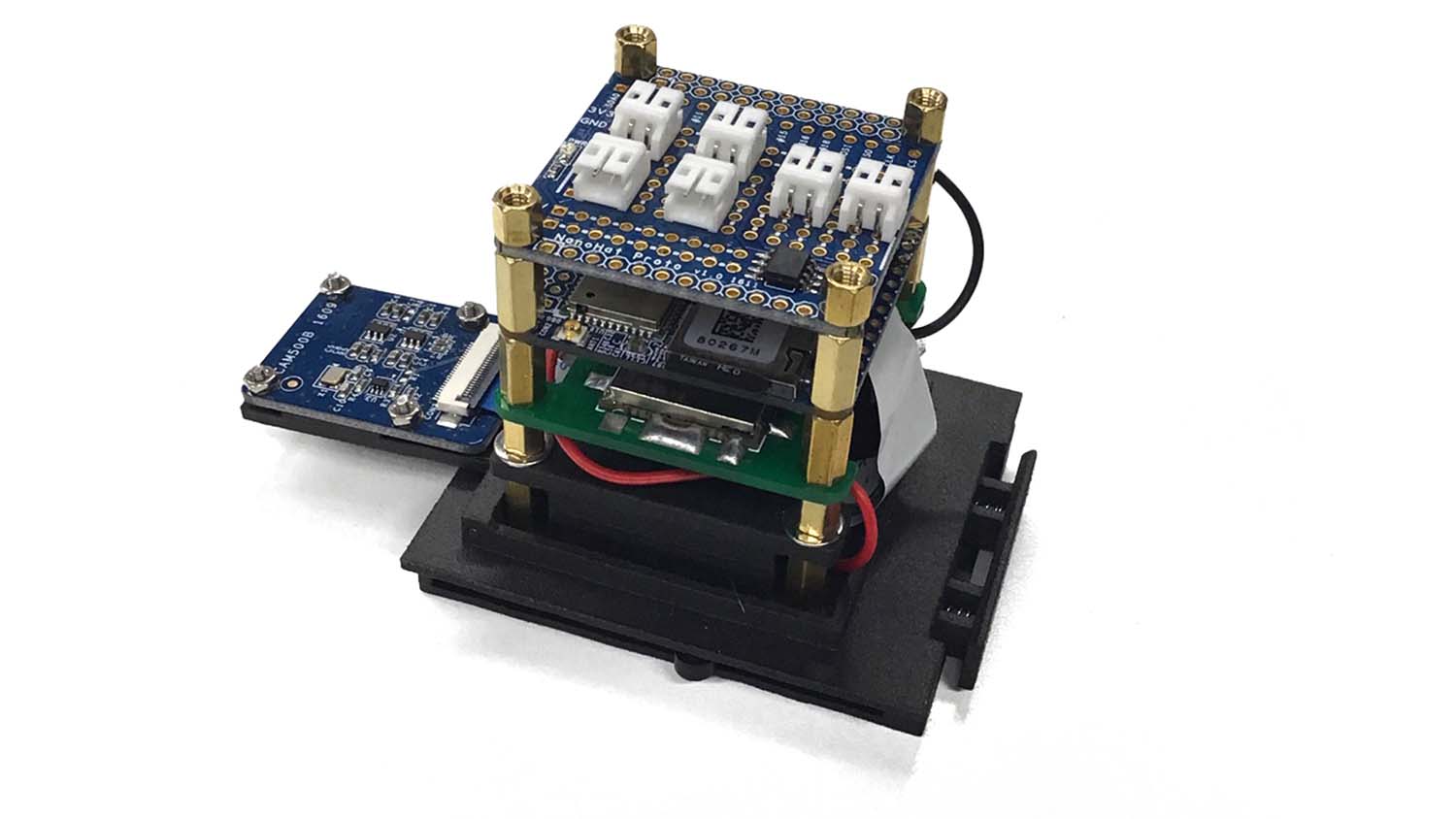
“Our particular satellite is a demonstration of what can be done for remote sensing of Earth’s resources on that scale,” says Latrell. “The challenge with something so small is to fit the electronics, camera, and radio system into it.”
He adds that this is the first time an entire satellite would be manufactured from a material like Windform XT 2.0, which came with risks.
“Performance is everything. If any one of the parts fail, it would result in complete failure of the spacecraft.”
However, there are big benefits to using a carbon reinforced nylon laser sintering material like Windform XT 2.0 for aerospace projects. As Latrell explains: “The combination of strength and ease of use made the material a natural choice for us.
“We knew we wanted to use additive manufacturing for Discovery but understood that it would be hard to find something that would work in the harsh environment of space. We discovered Windform XT 2.0 and after looking at its properties, it was a simple choice.”
Windform XT 2.0 features improvements in mechanical properties including +8% increase in tensile strength, +22% in tensile modulus, and a +46% increase in elongation at break over previous generations of Windform XT materials.
Interestingly, Windform XT 2.0 has passed outgassing tests by several space agencies and is already consider suitable for space missions.
CRP USA manufactured three 1P PocketQube functional prototypes for Mini-Cubes: two for testing and one for flight.
The 3D printed 1P PocketQube functional prototypes have successfully passed the control and testing criteria and have fully complied with Mini-Cubes’ standards.
“We have run quite a few tests with many more on the way. So far we have load tested to over 20 Kg. The material has been vibration tested to NASA GEVS-7000 specifications, subjected to a near vacuum to simulate the conditions in Earth orbit, and thermally tested from +50c to -40c. Windform XT 2.0 has passed every test we threw at it,” says Latrell.
He continues, “The next step for us is to test the satellite on orbit. This will be the final validation for our process. The plan is to launch sometime in Q2 2021.”
If you want to learn more about CubeSats, then the this European Space Agency video is a solid intro to the subject: