Moving away from Renishaw’s development centre in Stafforshire, the Welsh start-up Atherton Bikes, decided to invest in its own in-house AM equipment and has selected RenAM 500Q metal AM system, to enable a more flexibile design process for lighter, stronger parts
With its famous woodlands, valleys and mountains, Wales has firmly established itself as one of the best places in the world for mountain bike trails. And it’s in this heartland of the sport that Atherton Bikes has opened its first facility to develop bikes that employ 3D printed components combined with bespoke carbon fibre tubing.
Atherton Bikes’ design team is made up of World Championship-winning bikers who develop their own mountain bikes to be used in competition.
By putting to practice their experience and successes, they design and produce a range of bespoke bikes, which are sold globally.
Customers are able to try these bikes in the Atherton designed Dyfi Bike Park, where they can test the product on different terrains so that it can be fine-tuned according to the rider’s needs and preferences.
Flexibility is one of the greatest advantages of employing AM in the manufacturing process, as it allows the design team to create customised parts. Atherton’s bespoke bikes are in fact created according to the rider’s size and specific terrain requirements.
Manufacturing using traditional methods, like casting, says Atherton, was challenging because the size and racing style of each rider requires bespoke components to be made for each bike. Creating bespoke casts is often too costly and time-consuming, to be adopted for just one single part.
Another advantage of employing AM is that it allows producing parts which are stronger and lighter compared to traditional manufacturing methods. As the bespoke bike frames are adjusted during manufacturing, each surrounding component needs to be adapted to make the bike robust and durable, and this is not always easy with traditional methods.
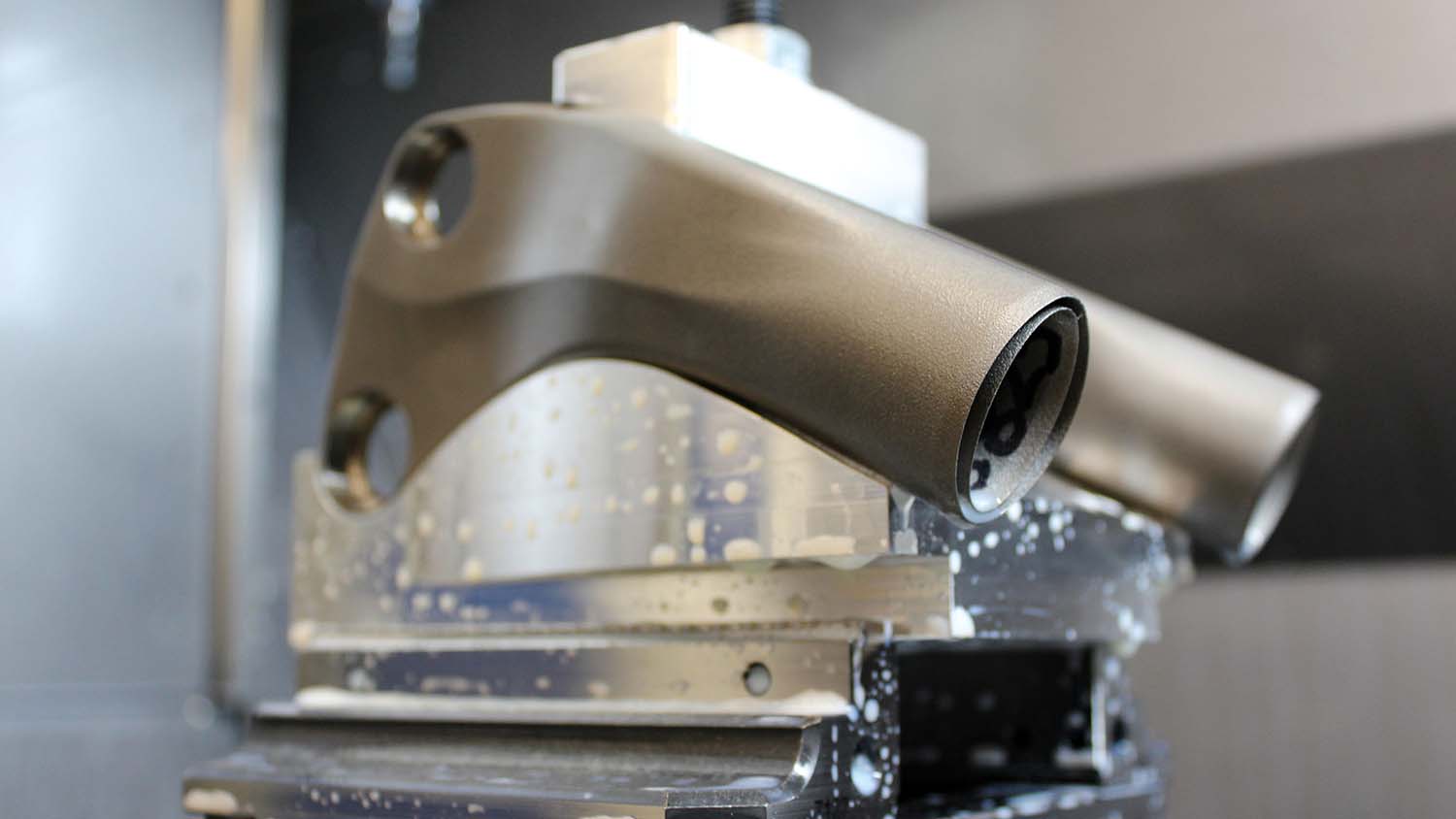
Manufacturing the lug, for example, was particularly challenging. This part reinforces the joints between tubes to help distribute stresses put on the bike while riding on harsh terrain.
Atherton was looking for a method to manufacture a robust lug that was also lightweight and found that AM was the only convenient method to obtain a part with those features as manufacturers can change its internal structure to reduce its weight, which is not possible with a traditional method like casting.
Moreover, subtractive methods require a large amount of tooling, which increases the production time for the bike, causing a challenge if there is a tight turn round before a race. Atherton required more rapid processes of manufacturing components.
Atherton also chose to use AM because of its fully digital process, which enables the team to easily modify bike lugs in CAD and produce bespoke components that are easy to reproduce.
The start-up has collaborated with Renishaw to develop its in-house additive manufacturing processes, having initially collaborated with the 3D printing experts to produce the components using its multi-laser RenAM 500Q metal AM system at its solutions centre in Staffordshire, England.
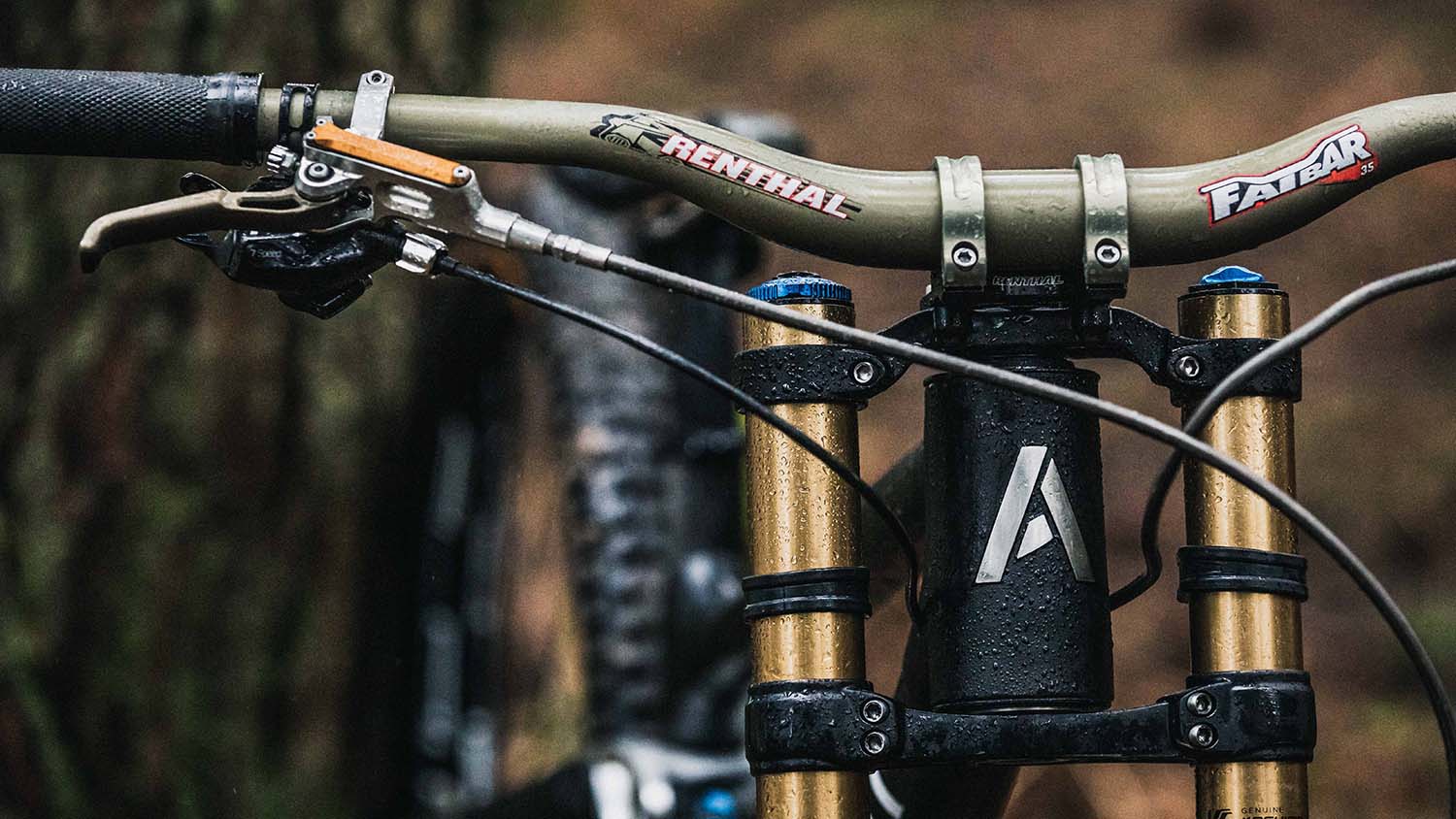
Atherton was able to collaborate with Renishaw’s team of specialists to hone the manufacturing techniques and the final product, modifying the process based on feedback from the riders as they tested the components.
After a few years of successful AM production, Atherton decided to take the leap and invest in an in-house facility, selecting the RenAM 500Q metal AM system and its relatively compact form.
“The RenAM 500Q has been an industry-leading machine for some time, so there was no question about the technology we were going to invest in because we had already built our business model around the system,” explains Atherton Bikes co-founder Dan Brown.
“The rapid and agile machine produces the capacity and high quality of lug sets that we require on a daily basis,” he goes on. “Atherton’s ongoing relationship with Renishaw has been great, especially during the initial in-house set-up period.”
Brown explains that, after the installation, part of the engineering team at Atherton went to the Renishaw site in New Mills, Gloucestershire to be trained on the new in-house facility, the health and safety protocols and the use of the software.
“Supporting Atherton through the initial design and prototyping and onto the race circuit and mass distribution has proven the bespoke and high demand manufacturing capabilities of the RenAM 500Q,” explains Renishaw director of sales Bryan Austin.
“Atherton’s newly installed machine and the support of our expert engineers will allow Atherton to continue its journey as an industry innovator and grow from strength to strength as its products continue to develop.”
Opening the new development centre to Machynlleth turned out to be a particularly successful move for Atherton Bikes, who said it received much positive feedback from its customers.
“Lots of our customers choose to pick up their bikes from our office and spend the day in the local bike park putting it to the test,” says Brown. “We are able to manufacture bikes in Wales and apply a level of care and detail similar to what our World-Champion winners would receive at the top of their careers.”
Adopting AM production technologies, thanks to the collaborations with Renishaw, turned out to be even more of an apt choice. Atherton Bikes says it allows to reduce the cost and time to produce bespoke parts, and creates a smooth, reliable, and more flexible process to meet any rider’s requirements and desires.