As NASA prepares to return to the moon with its Artemis mission, we speak with Aerojet Rocketdyne, a company that is modernising systems from the Apollo era to accelerate future moon missions
At Aerojet Rocketdyne, a producer of advanced propulsion space systems, engineers have optimised the design of a thruster module previously proven in space during the Apollo programme moon missions nearly 50 years ago.
Used to orient and propel the Orion crew module in space, not only is the new Reaction Control System (RCS) quad thruster 67% lighter, but it also helps reduce the overall production cost of the thruster by 66%, enabling fast, economical, and sustainable lunar exploration.
In preparation for NASA’s Artemis programme and other commercial efforts that aim to explore and colonise the moon, the engineering team redesigned the RCS module by leveraging the advancements of the five past decades in propulsion, design and manufacturing technologies.
Having already successfully demonstrated that 3D printing could help consolidate the assembly of the thruster’s injector block as a single component, the team needed to further optimise the design for weight and cost – making the 600-plus thrusters required to make an exploration effort the size of the Artemis mission economically viable.
The legacy design of the RCS module consisted of the four thrusters, a manifold that feeds the fuel and oxidiser, and a multi-part, thin-walled casing to piece everything together. James Horton, an aerospace engineer and mission architect at Aerojet Rocketdyne and his team identified many opportunities for improvement.
The ability to reduce the number of components through part and function consolidation immediately reduced the cost of assembly, while consolidation also reduced potential points of failure, increasing the system’s reliability.
Aerojet Rocketdyne’s engineers also decided to incorporate advancements in rocket propulsion technology to improve the system’s performance, adding a more reliable rocket fuel and oxidiser combination. This is easier to store during long space flights and requires less energy to prevent freezing, reducing the system’s overall energy consumption and weight.
Using nTopology, the design team successfully shelled the part on its first attempt. As a bonus, filets could be added to all edges to alleviate stress concentrations and improve the part’s fatigue strength.
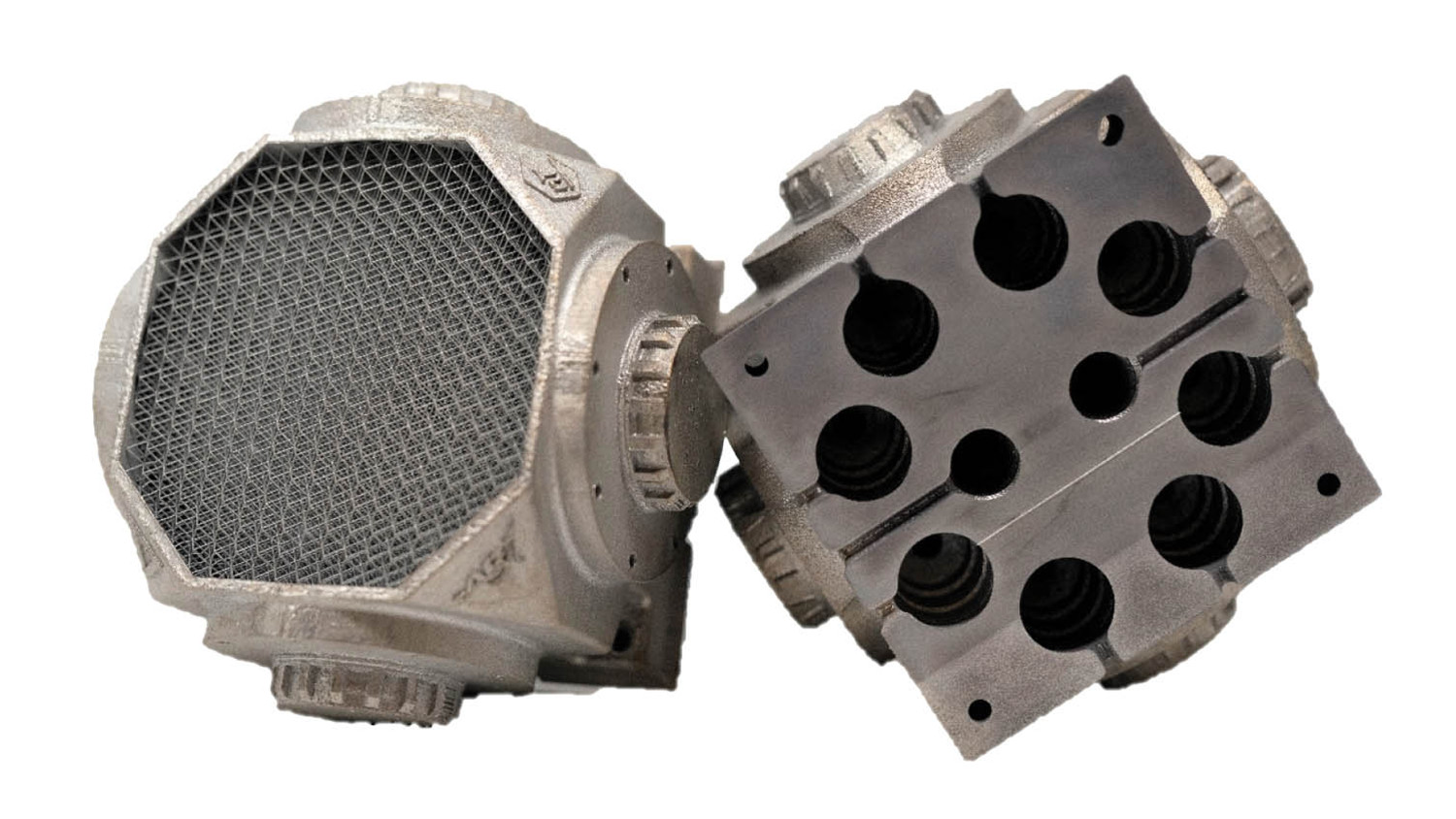
To further refine the structure, Horton’s team controlled key design parameters using nTopology’s field-driven design, allowing it to create a smooth transition in the lattice beam thickness — thinner in the centre and thicker near the shell — to further reduce the part’s weight. In a few hours, Aerojet Rocketdyne’s engineers were able to create a manufacturing-ready design candidate with a 2.5x factor of safety, based on the maximum tubing pressure.
The part was produced using a Velo3D Sapphire 3D printer in Titanium 6Al-4V. The material has approximately half the density of the Inconel 718 used to build the legacy part, helping to further reduce the thruster weight.
Caption (above image): Aerojet Rocketdyne is a key partner of NASA on preparations for the Artemis mission