Swedish product design agency Splitvision has spoken about its path to taking 3D printing in-house, and setting up an efficient workflow that makes having it in-house a benefit, and not a distraction.
With more than 30 years of experience in product development, Splitvision prides itself on its manufacturing knowledge for product design for injection moulded plastic with high functional and cosmetic demands.
Prototypes were previously made from Polyurethane foams or solid plastic materials to evaluate form and ergonomics, with more cosmetic models outsourced to either print shops in Sweden, or prototype services in China.
Splitvision brought additive manufacturing in-house in 2019 with the purchase of a 3D Systems Figure 4 DLP 3D printer, which it says instantaneously improved their additive process efficiencies, as well as the mechanical properties and fine feature details of their prototypes.
Since many of the products Splitvision develops and produces are for the hearing aid industry, parts typically comprise of a combination of both TPE and hard plastic, this was a deciding factor for DLP.
“We can now evaluate fit and assembly on a detail level before actually making the injection tools, typically saving us from 1-2 iterations of tool tuning,” explains Splitvision R&D director Lukass Legzdins.
“We also design casings for electronic products, and by using the Figure 4 printer to make small series production of those, it is possible for our customers to do field testing and user studies without investing in mass production tools.
While the Figure 4 3D printer has brought value to their workflow, bottlenecks still existed.
The post processing of parts created more problems than expected, including the excess labor needed to effectively clean more parts with more intricate details, and concerns regarding the smell and flammability of cleaning fluids in a design office space.
With parts like electronics casings, the intricate crevices like screw towers, small slots, and ribs make it a tedious job to fully clean resin from these features with a traditional solution like isopropyl alcohol, making the unit cost per-part unnecessarily high.
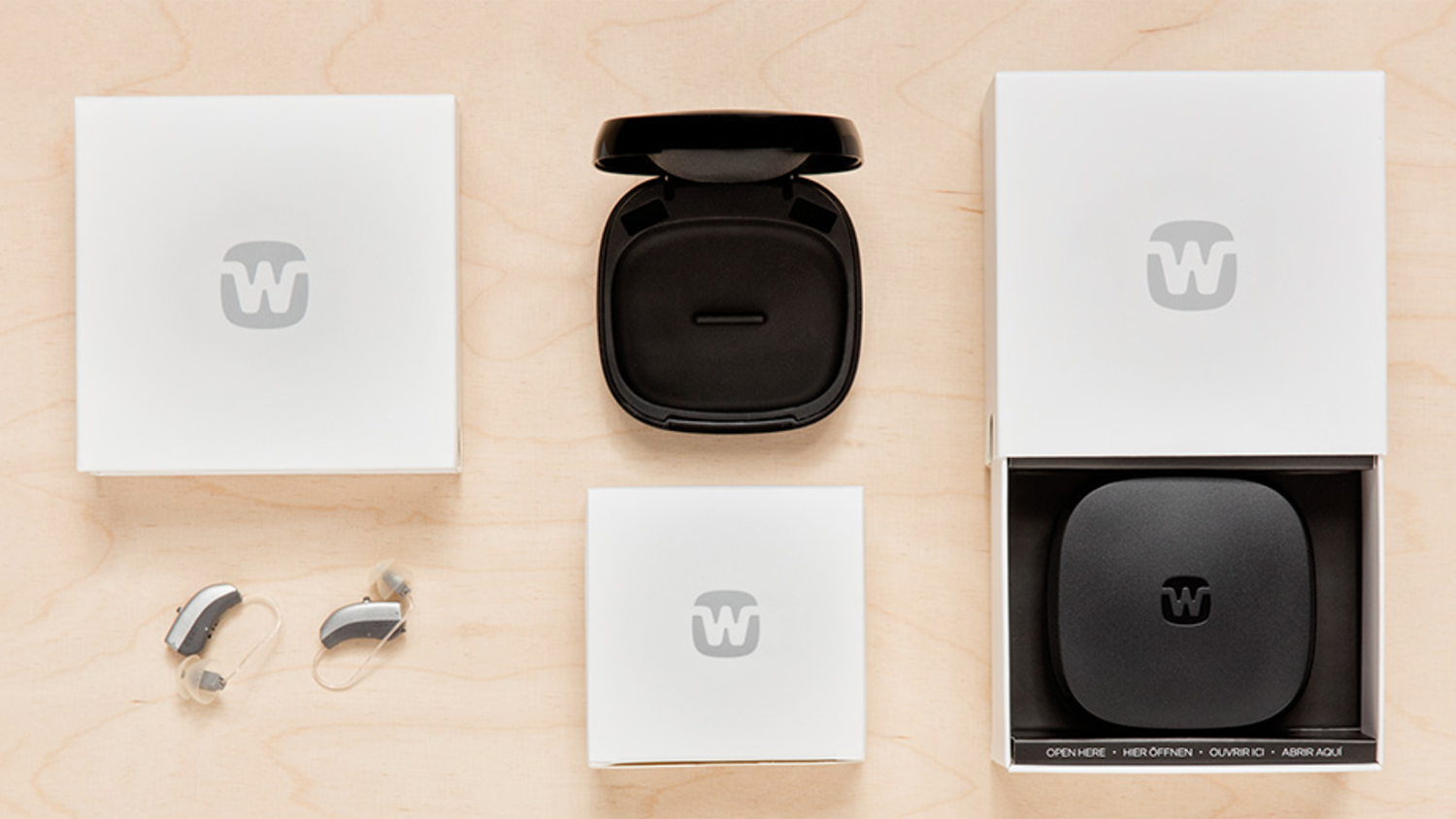
“Even if the printer used is efficient and several parts can be manufactured in one run, the unit cost still does not go down much since so much time is needed to clean each part individually,” explains Legzdins.
An automated solution was decided on, choosing PostProcess Technologies’ Resin Removal solution and proprietary detergent specifically developed for that system.
The Submersed Vortex Cavitation system uses ultrasonic cleaning and agitation, with controlled temperature for the process.
This has all the benefits as you’d expect from a good news customer story, but it offers some often unconsidered pointers too.
As well as Splitvision significantly reducing its post-printing cycle times, with a safer, and more pleasant working environment, individual electronics casings previously requiring up to 30 minutes each for resin removal are now processed in batches.
“Thanks to how efficient the PostProcess solution is within our workflow, we can now leave the support structure intact on parts when we need to do UV post-treatment of the DLP resin,” says Legzdins.
“This was never previously possible with traditional IPA cleaning because it was extremely difficult to get rid of all uncured resin behind the supports.
“An added bonus is that we can load printed parts into the PostProcess machine without ever removing them from the build tray, eliminating the need to clean the tray separately, removing another tedious process.”
Splitvision claims that each batch of 10 can now be processed in around five minutes with the PostProcess technology, which combined with the DLP 3D printing output speeds, means that the design studio can pass on time savings toward further iterations of parts in the design process, and to the customer.