Jewellery brand Eternha aims to combine traditional jewellery industry materials and craftsmanship with hi-tech polyamide-based composite materials, using CRP Technology tools and material
On a mission to blend hi-tech materials with fashion, the Italian brand Eternha designs jewellery with composite and polyamide-based materials used in the most advanced motorsport and aerospace applications.
It all started in 2020 when Stefano Massimiliano Marangoni lost a bracelet of great sentimental importance to him, and Chiara Cistriani decided to make him a new one using the same materials as the original.
Impressed by the result she achieved, Marangoni, who had a background in IT and Cistriani, an architecture graduate with experience in several different industries, decided to invest in their jewellery-making activity and eventually founded Eternha.
The concept was to produce jewellery using high quality materials such as Silver 925, surgical steel, together with hi-tech elements, which they achieve by employing the polyamide-based composite material, Windform GT, produced by CRP technology, and by using their Selective Laser Sintering 3D printing process.
“Our purpose has always been to realise high-quality jewels,” explain Marangoni and Cistriani. “Once the materials were fixed, we wanted to be innovative; so we decided to insert in our creations some elements made of a hi-tech material that, on the one hand, would provide a precise identity to our bracelets, and on the other hand, allow anyone to wear something unusual for the fashion world.”
Their fascination for the hi-tech industrial field does not only translate into the use of unusual materials for the jewellery industry, but it is also a visible in their designs. The shapes of the elements, they say, are inspired by geometric figures related to sport and technology.
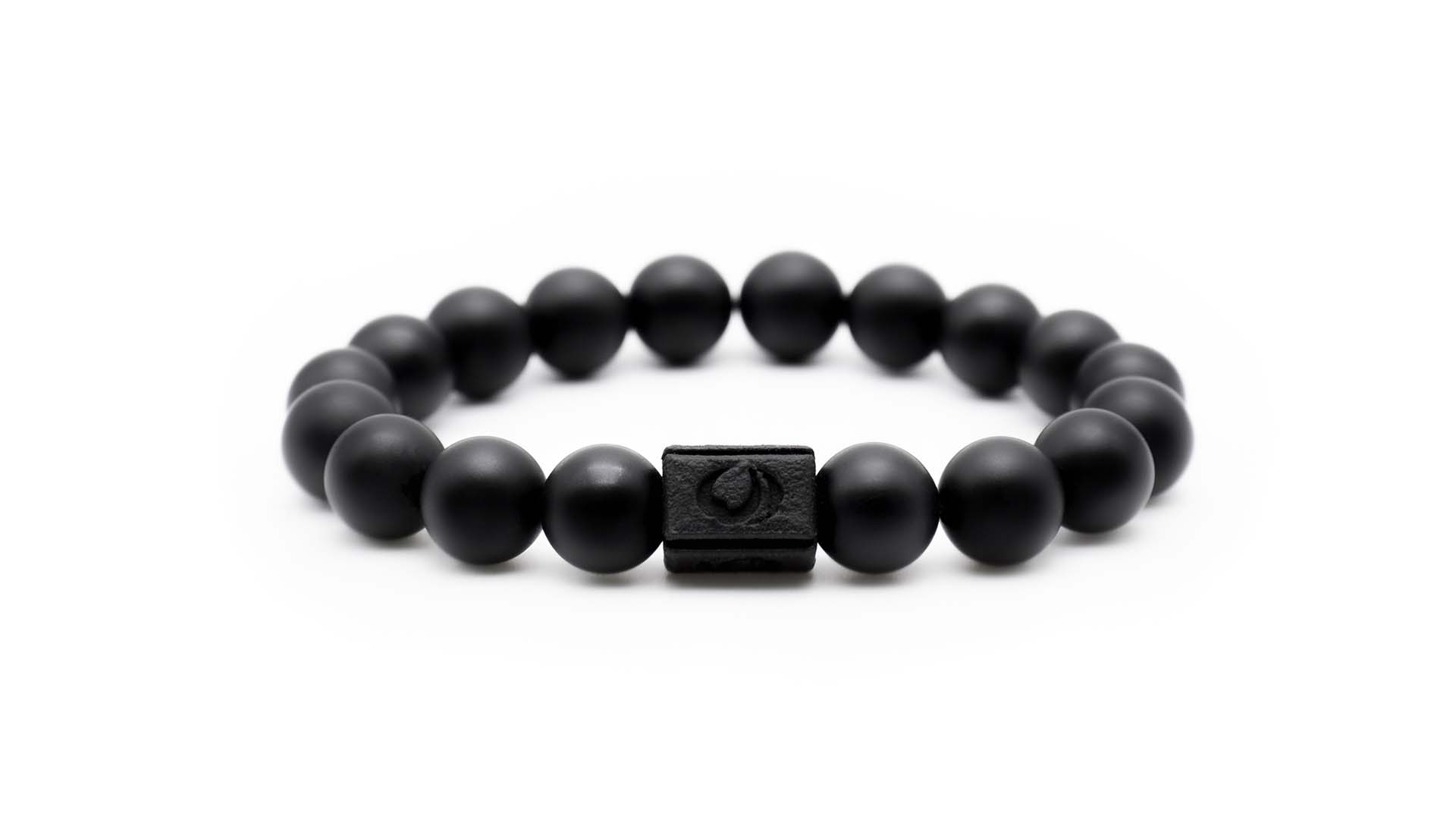
To help the pair realise their vision was CRP technology, which manufactured their elements using SLS AM technology and provided them with Windform GT manufacturing material.
Windform GT turned out to be the right material, especially for its resistance properties: “After having identified in CRP the appropriate technology supplier, we had to find the proper material for our aims; we liked the idea of combining our jewellery with indestructible elements, made of a material used for extreme and functional applications, something ‘eternal’.”
“We were looking for material suitable not only for prototypes but for functional, end-use parts. This is a versatile technology, a great alternative to injection moulding for low-production runs,” they go on.
Windform GT is a polyamide-based composite, glass fibre reinforced, developed and produced by CRP Technology, which has been used to manufacture, via Selective Laser Sintering, some elements for Eternha men’s bracelets.
“They are small elements,” explains Marangoni, “approximately 10-12 mm as a maximum size. Shapes vary from parallelepiped to sphere and cylinder, with different graphic elaborations. And, in one case, with the engraving of our company logo.”
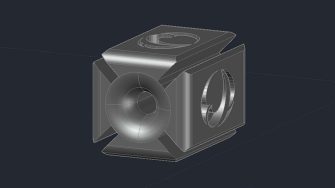
“Given the very small shapes,” takes over Cistriani, “we had to abandon some ideas and adapt others. But there is no compromise when it comes the quality. We wanted the top of the hi-tech range, and we got it with the Windform GT composite material.”
As Eternha designers explain, Windform GT is a highly versatile composite material in terms of performance and aesthetic appeal, as it combines excellent characteristics of elasticity, ductility and impact resistance, with a deep lustrous finish after hand polishing.
Additionally, it’s not electrically conductive, resistant to the absorption of moisture and liquids, and is approved for skin contact.
“We wanted to include in our creations one or more elements made of a material used to manufacture advanced, functional applications; a material capable of attracting customers for its intrinsic meaning and for the suggestions it evokes, rather than for its excellent mechanical characteristics,” explains Marangoni.
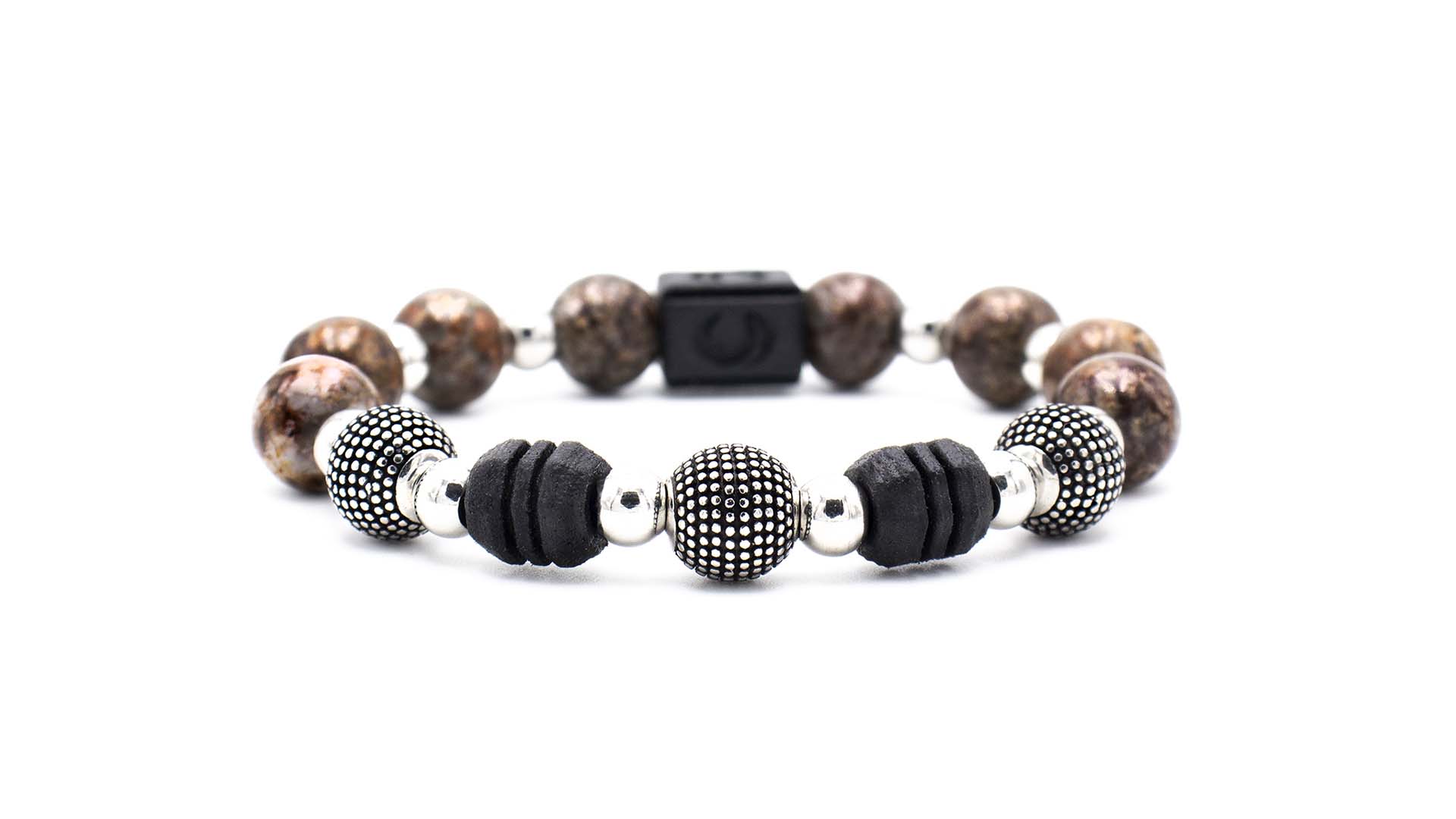
The design process starts with pencil and paper, which is “the perfect way to transform thoughts in reality.” They then move on to realise a 3D model using Blender, where they can mount the elements intended for the 3D printing, to make sure the product is balanced, the bracelets rotate, stretch, twist and achieves the desired aesthetics when worn on the wrist. Once they are satisfied with the 3D model, they send it to CRP technology for the AM manufacturing process.
3D printing is particularly advantageous as it guarantees total control of the concept, as there’s no risk the design is distorted during the manufacturing phase. This was central for Eternha, as their jewels are sold online only, and personalised with the wrist measurement entered by customers.
AM allows them to guarantee to their customers that what they’ll wear on their wrist is totally identical to the bracelet they have seen online, but made specifically for them.