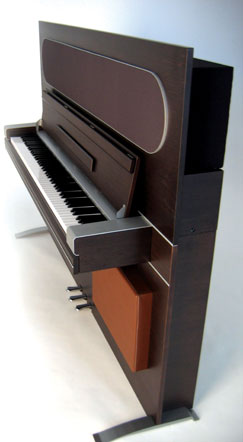
The MADE piano, even from its initial concept sketches, is heavily influenced by Italian furniture design
Korg isn’t all electronic noise, synthetic sound and dance breaks, it has an altogether more refined and classical side captured in its design – whatever music is being played.
With design offices around the globe, Korg Italy operates independently under the brand name from the town of Osimo, the traditional heartland of the old Italian music organ manufacturers. This heritage continues through the design team’s work on electronic pianos, organs and arrangers, key to the modern music industry.
Paolo Capeci, head of design at Korg Italy is quick to iterate that technology is at the heart of the products they produce. From a team of 35 based in their offices, only three, including Paolo, work on the actual design of products, overseeing everything from the initial sketches through to the packaging the pianos arrive in.
Perfect harmony
While Paolo immerses himself in design, his two compatriots work to blend the design with the engineering that lends Korg its position as high-end musical hardware. In contrast to the sleepy eastern province of Ancona, known for its traditional silk weaving, the rest of the office works to advance the software and technology that produces the digital sound.
“Most of the time we start from the boundaries of the mechanism,” says Paolo. “We use sketching to conceptualise design and ideas around this.” From here 2D sections are created, then a 3D model. Rapid prototyping is used in a variety of forms, however the adaptation to 3D CAD design means the Korg team are using it less, especially for aesthetic reasons.
“In this industry, specifically in designing digital pianos, the evolution is mostly inside the technology involved, and much less with the styling of the outside of the piano.”
Despite this, Korg offers an array of pianos that Paolo crafted to be desirable for more than just their musical credentials. “I was interested in designing a piano to fit in the living environment, interacting with our lifestyle,” explains Paolo, keen to show that as an Italian their office offers classic design principles to accompany the advanced technology. “We took the influence of the Italian experience in the furniture market, and exploring the possibility of different materials such as real wood, not just reproduction, steel, glass and leather.”
The end result was the Musical Advanced Design for Entertainment (MADE), the forerunner to the continuing line of elegant ‘lifestyle pianos’, designed to feel as beautiful as a piece of furniture, that can be used as part of the room, not an object set aside with the sole purpose of musical entertainment.
“We work simultaneously with different departments within Korg. The department in charge of styling works closely with the department in charge of the hardware and software, and the acoustics,” adding that projects are complex but by using software the different teams manage to model to requirements of the design. Paolo and his team design in SolidThinking, allowing them to pass design information back and forward between departments, making instant changes.
“It is extremely important for us to know what everyone else is doing, the requirements have a knock-on effect to all departments,” continues Paolo, adding that SolidThinking “allows us to manage the frequent design modifications that occur during the product development process.” Giving them control through all stages.
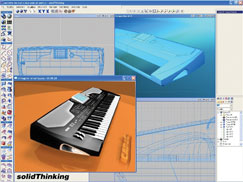
SolidThinking allows Korg to manage the frequent design modifications that occur during the product development process, as well as for rendering
“The capability to handle the modification so easily and effectively was a key factor for our choice. The program’s Construction Tree has great value to us,” continues Paolo, adding: “Design modifications do not worry us and instead we are encouraged to explore different possibilities. Now we are not just faster in our process but we have also improved the quality of our projects. Improving a detail to perfect it – even in an advanced phase – is not a problem.”
By working with 3D CAD the team bypasses the previous work model, with SolidThinking allowing them to jump directly to the screen with their sketches. It has other benefits. “Before adopting SolidThinking it was complex to deliver an accurate model with accurate geometry for engineering. Now it is easier to pass that data to the other engineers.
“The problem before SolidThinking was that we were using 2D AutoCAD, we found we were losing control of a project and could do little to make changes or edit,” he reflects. “Once the design was approved it was used to create the rendering in 3ds Max.
“At that point I was losing control because the engineering department created the 3D geometries from scratch and, when modifications were required (which in our field happens very often), they were taking the lead for such modifications,” essentially these interfered with his designs, says Paolo, meaning a great deal more work back at the drawing board. Through using 3D, however, these problems are addressed. “Today we can exchange the project more easily and changes are not something to be worried about. It controls that original design intent is not altered during the engineering phase.”
“Now the geometry is accurate, aiding the engineering and allowing the project to be shared. [Engineers] can interact in this way but not lose time, and at that point we are able to make a presentation of the product as it will be. We are creating renderings of the real model, not just from the initial sketch.”
Play it again… and again
Paolo finds that through working this way he can get more from a design. “You have the capability to create lots of ideas and choose from them. You have the capability now to log the ideas, although maybe not all of them are used in the same year, but they are then available to use and adapt.”
Generally, products begin life as a concept a year before becoming available. Korg’s multi-tasking professional arranger, the PA2X, is a great example of this refining process, tuned to cram as much as possible into a piece of kit right up until the last minute.
“It’s for professional musicians, with a mix of qualities,” points out Paolo, noting its array of sliders, knobs and drawbars, that set out its functional intent compared to the sleek lines of the MADE. “The sound is special as it is targeted at professional musicians.”
Importantly it features qualities needed in a professional arranger, but at the same time carrying the brand image. “They have to be perceived by the user to have good sound, but then look good. For the PA2X, from a design point of view there was a lot of attention in choosing the right materials: Wood, aluminium and steel – avoiding using a simple plastic for the body. It must stand up to a lot of time being used by the musician and being transported wherever they go.”
And they travel far. Professional musicians and composers take their kit everywhere, which is why Paolo has been busy designing carry cases to accompany the product. It seems Korg’s piano’s are ready for the long haul.
www.korg.com / www.solidthinking.com
An icon of the music industry, Korg explain how collaborative 3D design keeps them in tune