Since 1993, specialist German manufacturer No-Limit-Custom (NLC) has developed high-end custom motorcycles, including the Harley Davidson V-Rod, as well as building prototypes, small-series production and manufacturing moulds and tools.
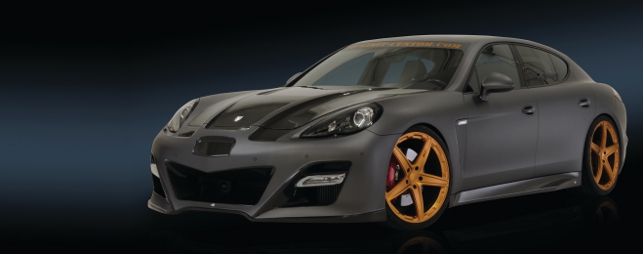
Project Panamera Turbo GP-970
With all this capability inhouse in early 2012 it decided to diversify into modifying sports cars, specifically Porsche.
For its first project, NLC has taken the Porsche Panamera Turbo and created a modification kit for it. Dubbed GP-970, the car has been completely restyled from the front skirt and hood to side skirts and roof spoiler to the rear skirt with integrated diffuser.
All parts are made from carbon fibre except for the burnished-gold forged alloys, which are custom made from high-strength aluminium.
From sketch to finished car
The philosophy of NLC is that where ever possible parts are designed, developed, and manufactured in-house.
The production of milled parts like wheels, rockers, and forks are made using several CAD/CAM stations and a machine pool with CNC turning and milling machines. So, when it came to the Panamera project, everything needed to manufacture the parts was under one roof.
However, help was required on the CAD side. As NLC’s CAD/CAM tools are provided by Tebis, it called on the help of Tebicon GmbH, a Germany-based Tebis consulting and implementation subsidiary.
In fact, some of the Tebicon employees who were helping on the project, based themselves at NLC for several weeks to work on the project.
Model making
Following the sketching stage, all the cutting, gluing and modelling is painstakingly done by hand.
A real model is then created with front skirt, rear skirt, side skirt, and hood. Only the right half of the model is finished as optimisation and the mirroring of relevant parts will be carried out later on the computer.
Using a GOM 3D scanner, the model is prepared for the virtual environment. In order for all details to be later converted, all individual parts are removed and digitised from every direction.
Reverse engineering
It was here that the Tebicon specialists could really get to work.
Using the Reverser, the Tebis module for rapid surface creation, the design surfaces are directly generated and optimised on the previously digitised right half of the model. When the surfaces and transitions are correct, the part is mirrored.
The Tebis Optimiser is then used to generate high-quality surfaces.
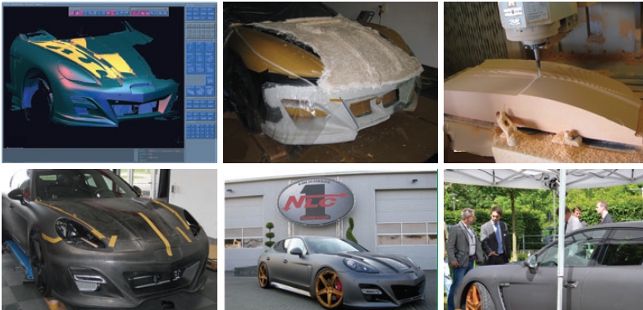
From sketch to finished car
Edges and unevenness visible on the mesh data now vanish and instead the model features clear lines, smooth edges, precisely fitting connections and an even progression of the light lines. Add-on parts and wheel rims are designed according to the design concepts of NLC.
Being a creative process, new ideas would frequently emerge ‘overnight’. So it was extremely helpful to have the project partner Tebicon directly on-site to quickly and precisely implement design modifications.
Milling and completion
The parts are then prepared for subsequent milling, and the NC programs are generated automatically using the Tebis CAM software and the integrated job manager.
The last part in the process involves milling the add-on parts in the in-house machine room.
With all these parts fitting seamlessly first time, the car is then painted and foiled. The end result is a combination of exposed carbon and grey base colour.
The GP-970 was presented at the Tebis Open House in Martinsried, Germany, towards the end of last year.
Since then NLC has unveiled its next restyling project: the Porsche Boxster S 981.
Tebis CAD/CAM tools aid specialist German manufacturer restyle sport-cars
Default