What if the key to progress lies in combining dazzling innovation with the ability to repair, repurpose and recycle a product? The breakthroughs could be astounding, writes Glen Smith of DriveWorks
In last month’s issue of DEVELOP3D, I was interested to read about the ‘right to repair’ legislation taking shape in many regions of the world. As you’ve probably gathered from my previous columns, I really enjoy building and making things. If something needs fixing or can be reused in some way, I’m your man.
Jaguar cars have always been my thing — from my first XJ6 that I bought for £600 using my student loan, to another XJ6, then an XJ8, a diesel XJ6, and now the all-new electric I-Pace.
But how things have changed when it comes to repairing our cars. I used my first Jag to drive my sister to church on her wedding day — and we only just made it!
I probably spent more time with my head in the Haynes Manual and under that car’s bonnet than I did driving it that day.
In fact, I had to persuade a friend to drive the bride and groom to their reception while I sorted out the Jag’s fuel pump. I then used up a two-week holiday completely rebuilding the inline-six engine.

Over time, however, I’ve been able to do less and less myself.
When I blew the engine on the XJ8, I soon learnt that it was a sealed unit, with few serviceable items. And the I-Pace motors are obviously sealed units too, with few mechanical parts.
Often, ‘new’ means ‘better’. We know that technology advances all the time. A car bought today will have far more built-in safety features than one designed 50 years ago.
My new I-Pace, for example, is smarter, safer, more streamlined and more ecofriendly than any Jaguar I’ve owned before. Everything on it, and in it, can be traced back to the original supplier and manufacturing process.
So back to one of my earlier themes: change happens, it happens for a reason and with safety in mind. Why would you want to cut corners, anyway? This new Jag is more complex than my first one and I’d be much more likely to damage it if I started tinkering around inside it.
That said, the Internet is a wonderful place. You can find a tutorial for pretty much anything.
Manufacturers are becoming savvy to this. I saw a story recently about Mat Armstrong, who rebuilt a crashed Bentley Continental GT and documented the whole build on YouTube.
Executives at Bentley saw the videos and offered a free health check to make sure it was safe before Mat’s planned journey to Monaco. The company’s technicians found over 100 issues with the car.
Contrast these cars with something that really was built to last. A couple of years back, I re-visited Wortley Top Forge, a water-driven iron forge near Sheffield.
This is where I first put my engineering knowledge to good use, working alongside my Dad, who had been a millwright for 40-plus years. It was a job that combined the skills of engineer, joiner, builder and designer.
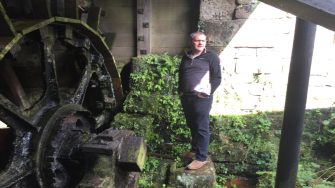
This old wheel, dating back to the seventeenth century, was built to last. It hadn’t turned for over 100 years, but after a complete strip down and rebuild, Dad and I had it turning again at 35 RPM, ready to generate the power to forge iron into railway axles, just as it had done as part of the powerhouse of the Industrial Revolution.
Cars and engineering aside, the last project I completed in lockdown was based on reusing and repurposing some sleepers and an old wooden staircase.
The staircase needed replacing, so I turned it into a pubstyle table with bench seating in my secret garden. I then used more of the treads for an outdoor planter for flowers, herbs and veg by the back door.
All it cost me was my time, but I gained a lot of satisfaction from planning, being creative and making something new.
At the start of 2020, I spent a day at the Science Museum in London. It was good to see old machinery like steam engines and massive turbines standing side by side with new technology such as driverless vehicles. But one thing that struck me was how technology took a big jump forward as a result of the two World Wars.
I’m no advocate for war or suffering, but history shows that when we face adversity, we do tend to innovate and make significant progress.
Right now, we’re already seeing rapid advances in virology, materials science, testing, analytics and remote communications as we wage our current war against the Coronavirus.
There is a balance to be struck here. What we need to do is to innovate on new technology, while still building in an ability to repair, repurpose and recycle. Maybe we need less glue and more bolts.
As my Dad often said, “Why use a nail, when four screws will do?”
Get in touch: Glen Smith is CEO of DriveWorks.
While we can’t condone the use of government-funded loans to buy Jaguars, we can confirm that one member of the D3D team spent most of his student loan on a kayak.
Get in touch at driveworks.co.uk or @driveworks