The FIA World Rally Championship (WRC) is for the hardcore motorsport fan. It pits cars and drivers in a series of two, three or four day races that take place not only over asphalt but over the snow and ice of Sweden, or the baking sands of Jordan’s desert.
The MINI WRC is powered by a 1.6-litre, four-cylinder Di turbo-charged engine
The cars competing at the top level of the sport are based on four-cylinder two-litre production models. But while they may look like your average high street car, these small hatchbacks are refitted to take on every dip, camber and roll.
Regardless of the road surface they can accelerate from a standing start to 100kph in around three seconds.
New direction
With nearly 27 years of experience in all types of motorsport, it’s rallying that is really at Prodrive’s heart.
This race engineering company has 100 international rally wins and six World Rally Championships under its belt thanks to its previous work with Subaru.
However, despite these successes, Subaru cars were retired from the sport by the manufacturer. So, following an inevitable downsizing at Prodrive, the new business plan was to find a manufacturer that would be willing to have its hatchbacks converted into rally cars that could be sold to enthusiasts around the world.
With this as the basic idea, Prodrive set about designing 3D models of potential cars.
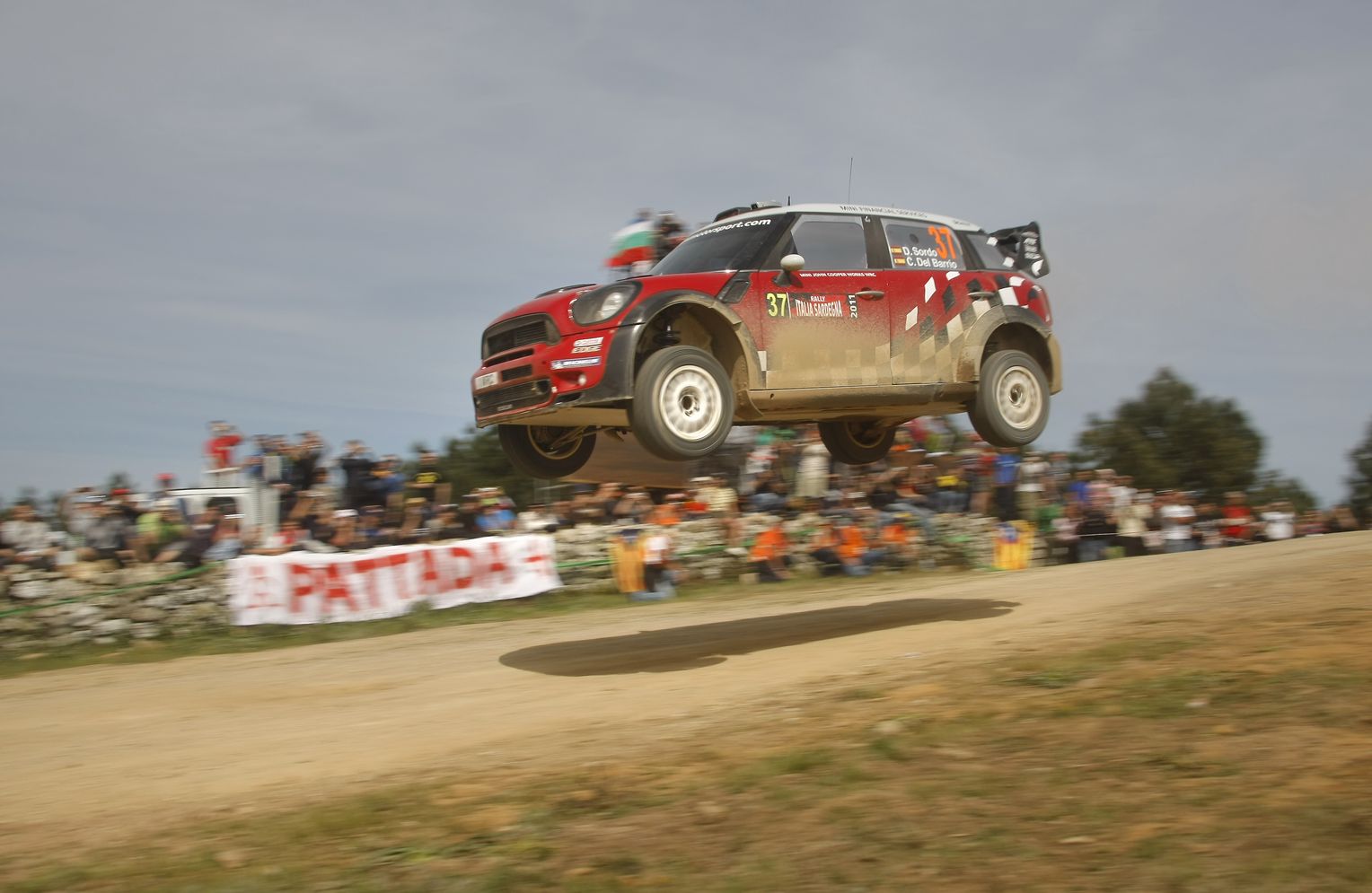
“We started off with a ‘generic car’ that we built as much parameterisation into as we could,” says Prodrive chief design engineer Paul Doe, standing by the open bonnet of one of the first customer MINIs to roll out of its facility in Banbury, Oxfordshire.
“It had to be as table-driven as it could, so from the top level we could switch between MINI and ‘Car B’ and ‘Car C’.”
Having a parametric model to work with was not new, but the need to have a 3D model that could slip between the dimensions of several possible cars using Excel data sheet tabulations was an invaluable tool at the development stage.
Having touted its wares to several possible manufacturers it became clear that BMW’s MINI was the pick of the bunch, with the German manufacturer keen to reciprocate the idea with its new Clubman model.
“This was the first car that was done 100 per cent virtually,” says Doe, appreciating that MINI gave them all its CAD data straight from the beginning, something that most manufacturers wouldn’t dream of.
Number crunching
A rally car is built up around data and calculations. “If you did some sort of flow chart of what information you need to start off with it’s amazing,” says Doe.
As he explains, where the front edge of the rear seat would exist in the road car, this marks the point where the roll cage can be. Then the main hoop of the roll cage sets where the driver can be. This then helps set where the controls will be.
Lastly, with the controls in place, the configuration of the braking system can be assessed.
“This can mean completely different solutions for the cars based on slight adjustments of data,” adds Doe.
Working through the design of over 3,000 components, the overwhelming majority not to be found on your standard MINI Clubman, Prodrive opted for a top-down ‘tree-style’ approach to the design process.
“We set up a lot of primary data and then pass that down to the assemblies below.
“We’re a much smaller unit [than when working with Subaru] and are very coherent in how we’re doing things,” explains Doe.
“Where you have the engine and the gearbox – two major streams of work – the main skeleton at the top is driving all of that and it’s that which says where the engine is and where the gearbox is.”
“Because those tables are managed in PLM it allowed decent visibility for everyone as to what we were doing and how we were going to do it, and it made sure everyone was doing things in the same kind of way.”
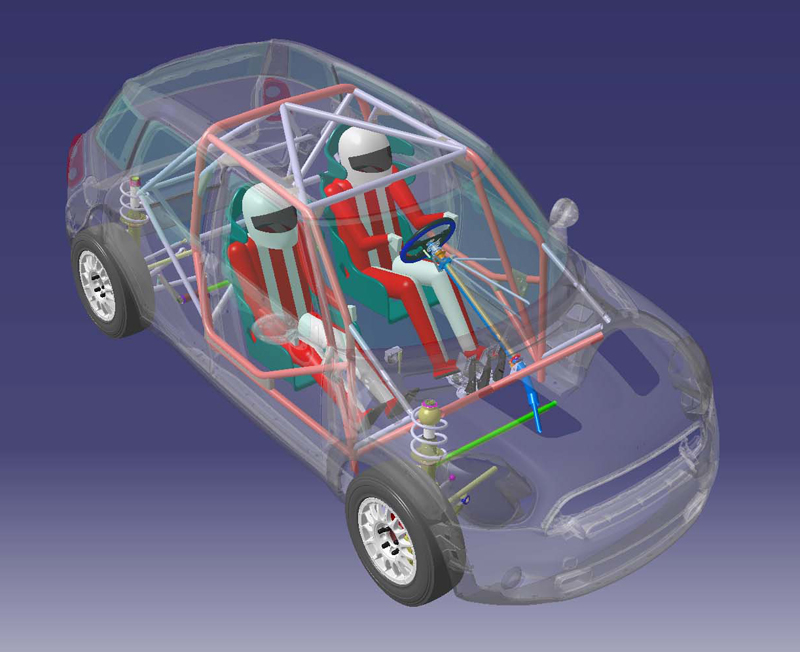
Utilising PTC’s Windchill PLM system to run and organise the project helped keep everything in line and on schedule.
“I would never want to be without it now, it’s another piece of technology that we’ve adopted for this project from the beginning, and it’s been another success,” says Doe.
“We’ve had a master model of the car, so everyone’s working off the same model and nobody’s overwriting anyone else’s work because it’s all controlled.”
As the team had more time to work on the car they were able to run FEA analysis through HyperWorks on the designs before they were signed off for manufacture.
“We have 12 load cases. They’re not real events, they’re generic events: a single wheel bump case with over 10G, then we see the effects, then we add that load case plus going through a corner, and then a pure cornering,” says calculations engineer Jonathan Culwick.
“I don’t think you could find an event or stage and say ‘there it is – those are the conditions we’ve modelled’. What I think you could do is say that these provide a ‘window’ where the car operates, and we protect the car in that ‘window’.”
At your service
One thing that sets rallying apart from other forms of motorsport is the need to be able to service just about everything on them in 20-30 minutes (a full gearbox can be replaced in little more than five minutes), with the only parts not allowed to be changed being the body shell and engine.
“It’s not just a case of making the car fast and cheap and all these things, but you’ve got to make it maintainable, which is where physical mock ups come in,” says Doe.
BMW sent the team a bodyshell and Prodrive installed a secondhand engine to transform it into a physical mock-up for hands-on testing using the CAD model as guidance. “You can do it virtually, but if you want to optimise everything you can’t escape a physical mock-up,” states Doe.
Under the bonnet the rally model is barely related to its road-going cousin: a giant turbo is bolted onto the engine to raise 300bhp, its dry-sump engine is much lower and further back in the bay, new ancillaries, manifolds, cooling systems , suspension turrets and stiffness braces are all positioned precisely for weight distribution and ease of access .
Rapid prototyping meant that parts for the mock-up engine bays could all be printed off and physically positioned well before the real mechanics had even arrived from the factory.
“We could have three or four different set ups and print the parts on the rapid prototyping machine, bolt them to the engine and build it up as an active engine bay and [the technicians] could start to spot problems,” says Doe. “We’d ask them to come and look at the CAD but they’d prefer to be touching, holding: ‘does the tool articulation fit?’ and all of those things.”
A giant drawer full of parts prototyped on the team’s Dimension SST1200es printer from its UK supplier Laser Lines is testament to how many iterations the team went through.
The race is on
With the MINI now successfully through its development stage, BMW increased its deal with Prodrive to include an official MINI WRC Team entry into the World Rally Championships for 2011.
“We all wanted there to be a factory rally team because it’s what creates the visibility and it really boosts the project,” says Doe.
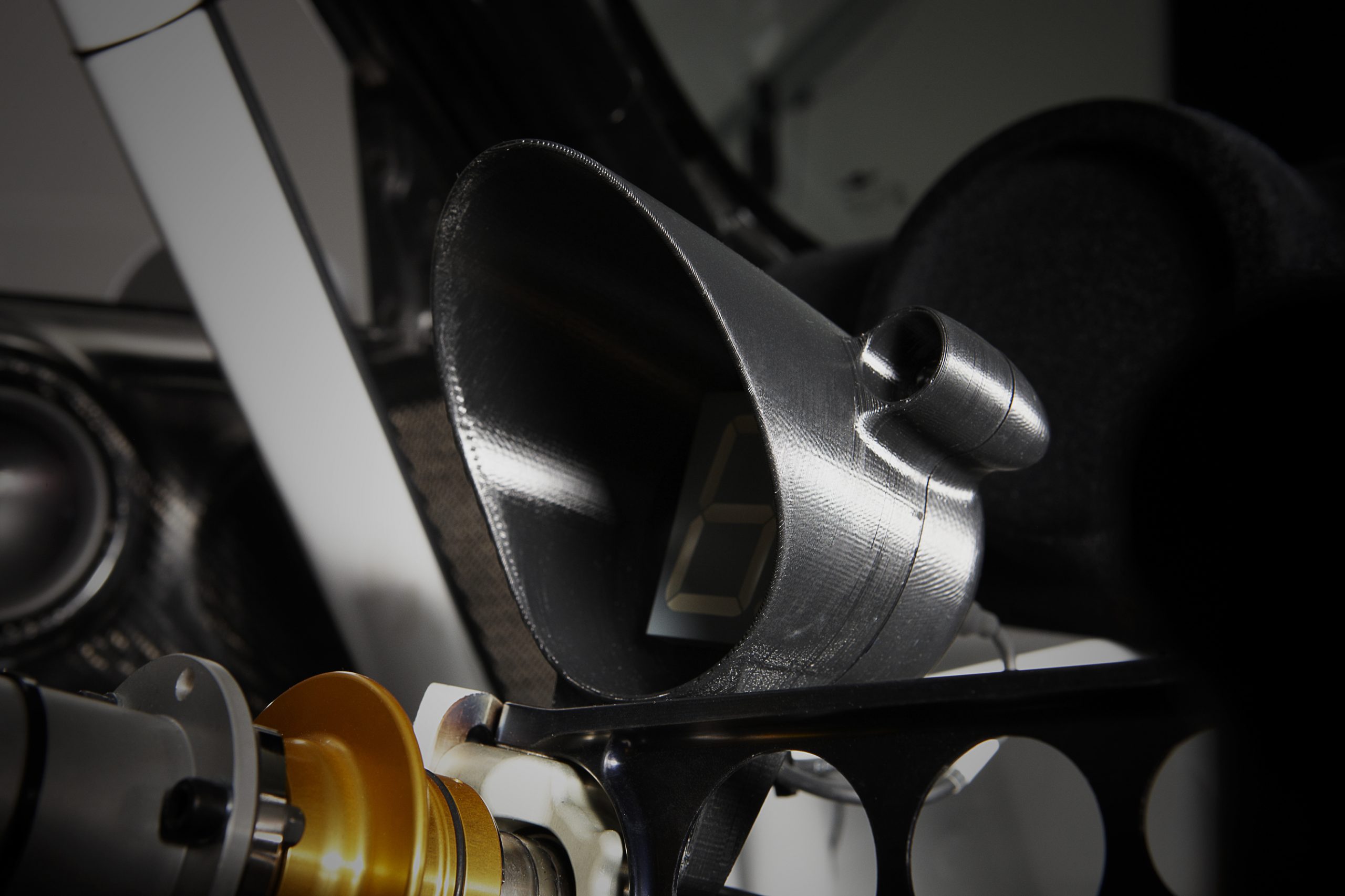
The amount of work that goes into each of the 8 factory and 20 customer cars is incredible, preparing each bodyshell takes hundreds of hours alone.
To help speed this up, Direct Digital Manufacturing (DDM) became a new buzz term around the workshops, and thanks to initial testing, the parts built through the FDM (Fused Deposition Modelling) technology were deemed strong enough to go straight into the cars.
With only eight factory team cars, the air duct covers, grills and breakers are all built up on the Dimension machine saving the time and cost of expensive tooling and moulding.
For Doe and the rest of the team it proved a short term solution that ended up being reliable enough to run with for real.
“Sometimes it’d be ‘we need something to go in here’ but it wasn’t really possible to get something made, so we’d model something up on the CAD and fire one off on the machine, in some cases in just a couple of hours, and have it fitted in the same night,” explains Doe.
“You can make a design that’s completely ‘unmanufacturable’ by normal methods, or at least not practically ‘manufacturable’. Instead of making it in five carbon pieces and then bonding them together, resulting in five patterns and moulds, we just design it and send it to the printer and it’s there and it works.”
Mainly the parts sent to the printer are those that don’t carry loads. The cars have a lot of rugged components, but also have a lot of parts that have no real stress on them that still need to be made somehow.
“A lot of the time we can’t justify not using it, which is odd!” states Doe. “We’re reaching a point of machine capacity now – there’s not often that the machine is sat idle, even though we’re fully through the prototyping phase. Now the machine is being utilised more than it was during the development phase.
“We have jobs that finish in the middle of the night and we’ve got 24 hour security, so we’ve trained all the guys on security how to swap the [printer build] plates over because it’s easy. You can send a print job over at 10pm from home, see that it’s finished and call up the guys and ask them to swap it over, and send through the next job so the next morning it’s finished.”
This has grown to the extent that the car now has a full parts list that is solely built on its Dimension printer.
As we step away from examining the 3D printer in the midst of another job, the two factory team cars are wheeled into the workshop fresh from competing in the Sardinian leg of the WRC.
At well over £300,000 each, these are specialist race bred machines with a fine pedigree coming from Prodrive, yet with an exciting future in the WRC thanks to the groundbreaking way in which the team is using the latest materials and technologies in their design.
www.minimotorsport.com
www.prodrive.com
A range of 3D printed parts within the MINI WRC
Airfilter
The lower ‘trumpet’ section on the huge airfilter was originally built as a feasibility mock-up part, with an eye to make it work for physical testing. “We did another model a bit thicker as we weren’t too sure how durable the material was, and that ran for the first two physical tests: it never went wrong, never cracked and we were impressed by that,” comments Prodrive chief design engineer Paul Doe.
Scuttlebox
This is like an airfilter for the passenger ventilation. Within it is a labyrinthine passage way to restrict any rainwater or other bits of debris from coming into the car. The complex nature meant it could be built as a single piece rather than five carbon fibre parts, with the extra expense that five sets of moulding would cost.
Rear arch extender
The motorsport governing body took a dislike to the MINI’s rear wheel arch: designed with an open rear to drag out hot air to help cool the rear brakes, they judged it illegal on the first of two days of examination.
Lips were printed off overnight stuck in place so, on the inspector’s return the following day, it was there and passed on the spot.
Bonnet air grill/vent shields
Only a few hours before the official launch of the cars to the world, BMW required a styling adjustment – a grill over the bonnet vent. A last minute print off done just in time, which was later amended for strength.
Computer screen holder
Customisable for height for each driver, this tray holds the information screen linked to the car’s ‘brain’. Drivers want it where they can see it and engineers want it low down for weight distribution – the printable case helps find the perfect compromise.
Speedometer/rev counter
Specially designed to be a product straight off the Dimension printer it consists of a large LCD display for showing gear/revs and its internal wiring components.